In the realm of industrial maintenance and machinery efficiency, selecting the right lubricant is not just a matter of choice—it’s a necessity. Especially under high load conditions, the proper lubricant plays a pivotal role in reducing wear and tear, enhancing performance, and extending the lifespan of machinery. However, with a plethora of lubrication solutions available, making the right choice can seem daunting. This guide aims to navigate companies through the complexities of selecting industrial lubricants, ensuring optimal performance even in the most demanding conditions.
Understanding Lubrication Needs
At its core, the primary function of a lubricant is to minimize direct contact between surfaces in motion, reducing friction and wear. In industrial settings, where machinery often operates under high loads, the choice of lubricant becomes critical. Factors such as operating temperatures, load pressures, speed, and environmental conditions significantly influence lubricant efficacy. Understanding these factors is the first step towards selecting a lubricant that can withstand the rigors of high-load applications, ensuring machinery reliability and longevity.
Types of Industrial Lubricants
Industrial lubricants come in various forms, each suited to specific applications and operating conditions. Oils, the most common type, offer excellent lubrication for a wide range of temperatures and conditions. Greases, which are oils thickened with soap or other agents, provide long-lasting lubrication where liquid oils would not suffice. Solid lubricants, such as graphite and molybdenum disulfide, are used in extreme conditions where conventional lubricants fail. Lastly, synthetic lubricants offer superior performance in extreme temperatures and pressures, making them ideal for high-load conditions. Understanding these types and their applications is crucial in selecting the right lubricant for your needs.
- Elevate Your Machinery’s Performance with JR Grasso Ordinario SOD – MP2: The Premium Multi-Purpose Sodium Grease
- Unleashing the Power of JR Olio Motore 20W50: The Ultimate Engine Protector
- Unleash Efficiency and Reliability with JR Olio Lub Per Catene: The Ultimate Chain Lubricant
- Unleashing Performance with JR Grasso Ad Alta Velocità: The Ultimate Guide
- Maximizing Performance with JR Lubrificante Adesivo-2500: A Comprehensive Guide
Selecting the Right Lubricant for High Load Conditions
Choosing the appropriate lubricant for high-load applications involves considering several key factors. Viscosity, the lubricant’s resistance to flow, must match the machinery’s operating conditions. Lubricants with the correct viscosity ensure a reliable lubricating film under high pressures and temperatures. Additives play a critical role in enhancing lubricant performance, offering properties like anti-wear, anti-corrosion, and oxidation resistance. The composition of the lubricant, whether mineral-based or synthetic, also affects its performance under load. Matching these lubricant properties with your machinery’s specific needs and operating conditions is essential for optimal performance and protection.
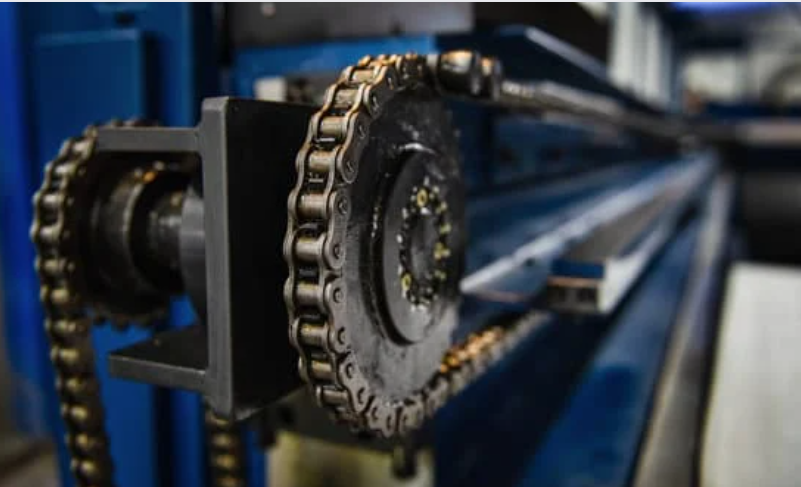
Best Practices in Lubricant Application and Maintenance
Applying and maintaining industrial lubricants effectively can significantly impact machinery performance and longevity. Regular monitoring of lubricant levels and conditions helps identify potential issues before they escalate into major problems. Implementing a lubrication schedule based on the manufacturer’s recommendations and operating conditions ensures that machinery is adequately lubricated at all times. Additionally, using the right application tools and techniques can prevent contamination and ensure that the lubricant is applied efficiently and effectively.
Real-world examples underscore the importance of selecting the right lubricant for high-load conditions. For instance, a manufacturing facility experiencing frequent bearing failures switched to a synthetic grease with high-load carrying capabilities, resulting in extended bearing life and reduced downtime. Another example involves a mining operation that adopted a high-viscosity oil with superior film strength for its heavy-duty equipment, significantly improving equipment reliability and operational efficiency.
Choosing the right industrial lubricant for high-load conditions is a strategic decision that can significantly impact machinery performance and operational costs. By understanding lubrication needs, exploring the types of lubricants available, and selecting a product based on specific machinery requirements and operating conditions, companies can ensure their equipment operates smoothly and efficiently. Consulting with lubricant experts and adhering to best practices in lubricant application and maintenance further enhance machinery reliability and longevity. As the industrial landscape evolves, staying informed and making educated lubricant selections will continue to be a cornerstone of successful machinery management.